Supply chain woes leading to profit losses for UK construction
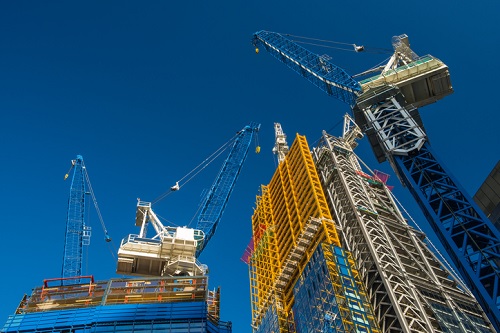
Authored by QBE
Three in five (59%) UK construction companies that have been hit by supply chain issues over the past year have seen once profitable projects turning unprofitable, research from business insurer QBE has found.
In a survey of senior leaders in the construction industry*, 83% said they had experienced an issue with their supply chain over the past 12 months, while 85% said that they expected supply chain issues to pose a challenge in the next 12 months.
85% said that the cost of importing construction materials increased at a rate higher than inflation over the past year.
According to a new report from QBE Business Insurance in partnership with Oxford Economics and Control Risks, Supply Chains and the UK Construction Sector, the outlook for the UK construction industry in 2023 is likely to be equally as disruptive as 2022. Geopolitics and domestic developments will continue to affect access to materials and their price.
Since the first pandemic lockdown, a shortage of materials has been the largest factor constraining construction activity in UK. Nine out of 10 (89%) of respondents impacted by supply chain issues said that they were currently experiencing a shortage of materials.
Andy Kane, portfolio manager, construction, QBE International said: “Construction firms in the UK have seen continuing shortage of materials and supply chain disruption since the start of the pandemic. Therefore, it is no surprise that the majority of those we surveyed have seen disruption which has ultimately impacted profitability. With these challenges set to continue throughout most of 2023, now is the time to take action to limit disruption and protect profitability.”
He continued: “There are steps that construction industry leaders can take in order to lower their supply chain risk. This includes shifting away from the “just in time” supply chain model we have witnessed in recent years to a “just in case” supply chain.”
In addition, businesses can take steps such as using technology to automatically order supplies when stock levels go below a certain point, look to diversify suppliers and, where higher input prices are the likely fallout from supply chain disruption, consider adding a cost escalation clause to future contracts.
Many of the construction firms surveyed said they taking steps such as diversifying supply chains (42%), holding greater stocks of strategically important materials (31%), establishing robust monitoring systems of stocks and suppliers (23%) and nearshoring (17%), however the survey found nearly one fifth 18% have not taken any action.