Green Hydrogen: Innovation and Obsolescence
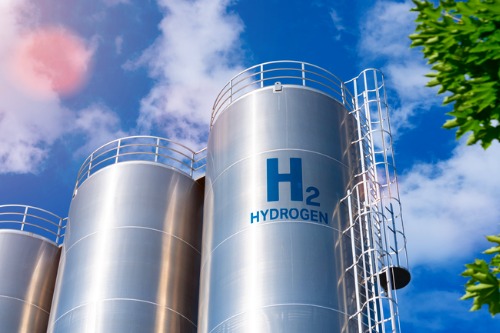
Authored by Liberty Principal Risk Engineer, London, Arthur Delargy
In my last article, I focused on the challenges that incumbent electrolyser Original Equipment Manufacturers (OEMs) face in scaling up production capacity to meet the expected rapid increase in demand for green hydrogen in the coming decade. The focus was on alkaline water electrolysers (AWEs) and Proton Exchange Membrane (PEM) electrolysers, which are already commercialised. Existing electrolyser products have been designed for the demands of industries such as chlor-alkali manufacture. Large scale green hydrogen production is a new scenario and requires new demands on the electrolyser, with the potential for significant technological innovation.
Innovation Focus: Advancements in Electrolyser Technologies
The pace of innovation in alkaline and PEM electrolysis has been rapid in recent years. Costs continue to fall, and efficiencies are rising. Stack architecture is undergoing a radical transformation, manufacturing methods are evolving, and electrode designs are migrating to lower-cost, earth-abundant materials.
In the world of alkaline electrolysis, OEMs include established players that have been manufacturing electrolysers for 100+ MW projects for decades. A large cluster of recent, mainly Chinese entrants, is also on the list.
The main areas of innovation are around:
Increasing the current density to increase system efficiencyEnhancing operating flexibility to respond to renewable energy power fluctuations Increasing operating pressure to simplify downstream compression requirementsUsing differential pressure cells which allows for lower-cost components on the oxygen side
Stargate Hydrogen, an AWE manufacturer based in Estonia, has developed a patented ceramic catalyst that maximises the current density in alkali electrolyser stacks, allowing reduction in stack size, due to be installed at a site in Tallinn in 2024.
A number of manufacturers are also focusing on pressurized alkali water electrolyser (PAWE) designs, including HydrogenPro (50 barg operating pressure) and Green Hydrogen Systems (35 barg operating pressure).
Dutch innovator Newes Hydrogen has developed a system that can operate at up to 350 barg, with a 1 MW demonstration unit due to go into operation in 2024.
Canadian developer, Hydrogen Optimized, has developed the Unipolar RuggedCell™Alkali Electrolyser technology that can operate over the full dynamic range of available power, and is designed to allow operation of a few large (50MW+) electrolyser modules using a patented Current Carrier Frame design.
For PEM electrolysers, technology innovation will focus on improved manufacturing techniques for key components such as membrane electrode assemblies (MEA) and bipolar plates, including developing larger and thinner membranes, together with lower loading of platinum group metals to drive down costs.
H2U Technologies has developed an iridium-free PEM electrolyser in collaboration with CALTECH, using AI-assisted data mining to synthesise, screen and characterize multiple catalyst combinations.
The Electric Hydrogen Company (EH2) has developed a breakthrough PEM electrolyser by developing proprietary cell and stack designs, which “push the power density to unprecedented levels for commercial scale”, leading to a compact, lower CAPEX unit.
The rise of challenger electrolyser technologies
And then come the challenger technologies. Anion Exchange Membrane (AEM) and Solid Oxide Electrolyser Cells (SOEC) are on the rise, with a number of companies developing the technology and some commercial deployments. AEM technology combines the advantages of PEM and AWE electrolysis and is close to commercial implementation. AEM membrane innovation will see the stack life improve, stack sizes increase and costs of ownership decline. For example, in early 2024 Ohio-based Power to Hydrogen (P2H2) successfully demonstrated a fully integrated electrolysis system pilot using its patented AEM stack, which is already four times larger than any commercially installed AEM stack.
Solid oxide electrolysis is the preferred green hydrogen production method for e-fuels and green ammonia integration since heat from downstream reactions such as ammonia synthesis, methanol production and Fischer Tropsch fuels produce excess steam, which can be used for the high temperature SOEC operation. But the technology still needs to scale and become more robust and durable to be bankable.
In each technology cluster, there are new entrants that have implemented an initial demonstration project of their pre-commercial electrolyser system and emerging startups that are raising series A or B capital. Among AEM manufacturers, Enapter and others have been joined by new players such as Cipher Neutron and Power H2. SOEC players have also multiplied, with established names like Bloom Energy being joined by many new arrivals such as Advanced Ionics who have created a hybrid SOEC design, which conducts oxygen ions between electrodes but does not feature a brittle ceramic membrane.
Added to this, there are technology disruptors that do not easily ‘fit’ in the established four technology boxes.
These are ones to watch and include:
Hysata, who have developed the Capillary-Fed Electrolyser (CFE), using capillary action to overcome mass transfer resistance to produce bubble free hydrogen and oxygen at 98% cell efficiency. A number of companies working on membraneless or membrane-free electrolysers. This includes CPH2, a UK company who has developed a water electrolysis technology that separates hydrogen and oxygen through cryogenics without the use of membranes. Membraneless electrolysers allow for the possibility of an impurity-tolerant device that can operate on tap water, eliminating the cost of water purification and enabling lower cost materials to be used in the balance of plant systems.The UK start-up Supercritical Solutions developed a high temperature, high pressure electrolysers using pressurised water, which claims to be more thermally robust and offers a superior stack life expectancy to SOEC designs.Israeli start-up H2Pro has developed a high pressure (45 barg) Electrochemical, Thermally Activated Chemical (E-TAC) electrolyser, which decouples the hydrogen and oxygen evolution reactions into two consecutive steps, ensuring hydrogen and oxygen never mix, and eliminating the need for a membrane.
There is also considerable research among academic institutions and developers in the area of saltwater electrolysis, which may be unlock additional sources such as offshore hydrogen generation on floating wind turbines and arid coastal regions with ideal wind and solar conditions. Nanjing Tech University in China is one of the pioneers of this work together with tech start-up Aeon Blue Technologies.
Based on the foregoing discussion, it is obvious that even so-called mature electrolyser technology may be considered as prototypical by the insurance industry, as it is deployed at scale and with variable renewable energy supply. These “Gen 2.0” PEM and AWE electrolysers, will likely be enhanced or upgraded at a later date to optimize and increase performance, similar to wind turbines with iterative cycles of upgrades, certification and series maturity. Some of the modifications to improve performance will also introduce new risks – e.g. thinner membranes or higher operating pressures increasing damage, cross-over and explosion risks.
Navigating the Competitive Landscape
As with any new or fast developing technology, “change is here to stay”. The hydrogen industry continues to see new entrants and potential ‘breakthrough technologies”, as reflected in our own electrolyser database, which now lists and ranks over 100 OEMs. There is therefore a significant risk that new types of electrolyser could render first mover technology obsolete, and so insured equipment can be rendered redundant. Some industry experts believe that PEM technology in particular could become obsolete with the rise of AEM technology and its more resilient supply chains, including reduced dependency on critical minerals.
In order not to lose the competitive advantage in such a crowded market, OEMs may also release early versions of their products to stay ahead of the competition and secure additional funding. Based on previous experience in the wind and solar industries, rushing a product to market without appropriate certification or QA/QC will increase the likelihood of insurance claims. Defects in design, materials, manufacture or erection are more common with prototypes. Related to this is the extent to which electrolyser modules supplied by different vendors are compatible with each other and the impact this will have on replacement times or exposure to one specific supplier.
The current level of innovation within the hydrogen industry may necessitate further mergers of successful competitors to provide longer term efficient designs. For example, emerging tech companies may need to either buy or, be taken over by, a competitor in order to access advantageous IP to secure superior market position. Traditional equipment manufacturers are more likely to be in a better position to both scale-up proven and implement unproven technologies than disruptors (or those OEMs relatively new to the industry).
The landscape for the green hydrogen market is very crowded, with a combination of experienced OEMs and innovators. The industry is a long way from being able to offer a “standardized product,” meaning that early projects carry unique insurability risks.
There are parallels between this and the emerging solar and wind market of 20+ years ago. In the early 2000s there were around 100 solar manufacturers. Of course, history has shown that 90% failed, and this may well be no different with electrolyser manufacturers. Some established OEMs are already facing financial challenges, partly down to over-extension to be first to market, or through offering a unique but non-replicable solution – e.g. where units have unique operating conditions so that unit replacement following an indemnifiable event could result in significant business interruption exposure. Other new entrants, including disrupters, are facing challenges in commercialising their technology offerings. As a result, we expect a brutal shakeout in the industry in the coming years as the winners emerge.
At Liberty, our longstanding underwriting, claims and risk engineering expertise allow us to support existing and prospective clients through this rapidly evolving landscape.