3 reasons why electric cars will soon get a lot cheaper
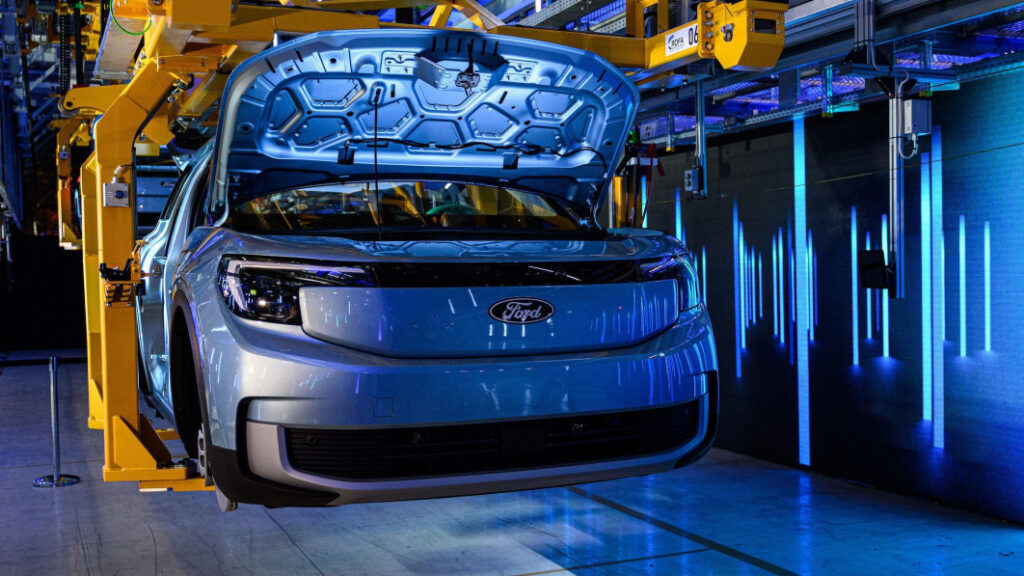
Automakers such as Ford have slowed down EV production over stalling demand. Lukas Schulze/Getty Images
Some automakers are slowing down EV production, saying electric vehicles are too expensive.
They have a point, with drivers looking to buy an EV having to pay a hefty premium.
But new batteries, production methods, and improved charging networks mean prices are set to drop.
EVs have an affordability problem.
There just aren’t very many cheap options – with the average price hovering just over $50,00 in September, according to Kelley Blue Book data.
Auto execs have pointed to high prices as a big reason why demand for electric cars has slumped this year.
Several have slowed down their EV plans as a result, with Ford postponing a $12 billion investment and General Motors abandoning plans to build 500,000 EVs by the first half of 2024.
All this, however, may be about to change soon. EV sales are on the rise, with more than 1 million electric vehicles expected to be sold in the U.S. this year, taking a record 9% of the passenger car market, according to Atlas Public Policy.
That share is still well behind other countries, with EVs reaching 33% of sales in China and 35% in Germany in the first three months of 2023, according to Bloomberg data.
Tesla is reportedly planning to put a 25,000 euro ($27,000) car into production next year, and a number of fast-moving developments in the technology behind electric vehicles may soon see prices plummet.
Goldman Sachs even thinks EVs will hit price parity with gas-powered cars by the middle of this decade.
Here’s three reasons why electric cars are getting more affordable.
1. Cheaper battery packs
By far the most expensive part of any EV is the battery, and spiking battery prices have hit automakers hard.
However, the long-term trend is still heading towards cheaper battery packs.
Prices may have risen in 2022, but the Department of Energy estimates that the price of a lithium-ion battery pack dropped by 89% between 2008 and 2022, and Goldman Sachs says that prices for batteries will fall a further 40% by 2025.
“The battery is the single biggest cost going into electric vehicles and it’s subject to the same kind of technology price curves that you see elsewhere,” David Browne, the UK chief of EV manufacturer Smart, told Business Insider.
A Rivian charging at an EV charging station. Patrick T. Fallon/Getty Images
Leading the charge is the development of new classes of EV batteries, including sodium-ion batteries, which are more sustainable and cost-effective than power cells based on lithium. And, solid-state batteries, which are lighter and have more range.
In October, Toyota announced a breakthrough in solid-state technology that it said would allow it to halve the weight of its batteries by the late 2020s. Manufacturers think there are more breakthroughs to be made.
“We’re only scratching the surface in battery development,” said Browne.
“Working with ICE engines, you were chasing the smallest improvement in efficiency because people had been working on it for over a hundred years,” he said.
“But battery technology is moving so quickly, and there are so many exciting developments, that there is lots we can do to improve efficiency,” he added.
2. More charging points
Another speed bump in the road to mass EV adoption is the U.S. charging network, which is still patchy even in big cities such as Los Angeles.
Matthias Preindl, a professor of electrical engineering at Columbia University, told BI that boosting charging networks would allow manufacturers to put less emphasis on powerful range-boosting batteries, making their vehicles lighter and cheaper to produce – and in turn, meaning lower prices for the consumer.
Tesla’s North American Charging Standard and the CSS network are the two major charging networks operating in the U.S.
A Tesla charging station. Smith Collection/Gado/Getty Images
Tesla’s network is expanding rapidly, with the company planning to double the number of chargers it offers by 2024. It is also becoming the industry standard, with both Ford and GM announcing that their EVs will use Tesla superchargers from 2024 — something Cox Automotive director Stephanie Valdez Streaty believes will help boost the U.S. charging infrastructure.
“From an adoption standpoint, a consumer really wants to have that same experience as they do with an ICE (internal combustion engine vehicle), where it’s never a barrier,” she told BI.
“I think the key thing when it comes to charging infrastructure is going to be standardization,” she said.
3. Economies of scale
One key headache for automotive companies is that the best way to bring down the cost of making EVs is to produce more of them.
“You have to get to a certain scale to really start to make money on electric cars and for the costs to go down,” Valdez Streaty said.
“You begin to see more innovation and improved efficiencies in the manufacturing process,” she added.
That’s an issue for legacy automakers, who have increasingly moved to cut EV production targets in the face of slowing demand.
Some companies such as Tesla are bringing down costs by changing how they mass produce their cars, with Elon Musk’s firm pioneering a new process called “gigacasting” that allows it to produce large parts of a car’s body through molten metal poured into high-pressure molds.
The Tesla dashboard Chicago Tribune / Getty
Other firms like Toyota are racing to adopt similar methods, which allow manufacturing plants to produce cars that are both lighter and cheaper.
However, there are concerns that the new method could make it harder to replace car parts, and Browne said that while Tesla’s tactics are good for keeping costs down, they could lead to a spike in repair costs.
“The trade-off is if you’ve got one big mega casting down the side of the car and somebody damages that, you’ve then got an issue with repair costs,” he said.
Alongside new production techniques, major automakers are still expanding their EV assembly lines, even if they aren’t doing it quite as quickly — and that is good news for EV prices.
“I think one of the challenges that we’re seeing is that we’re still ramping up EV production. So as production increases we will see prices also decreasing long-term,” said Preindl.